
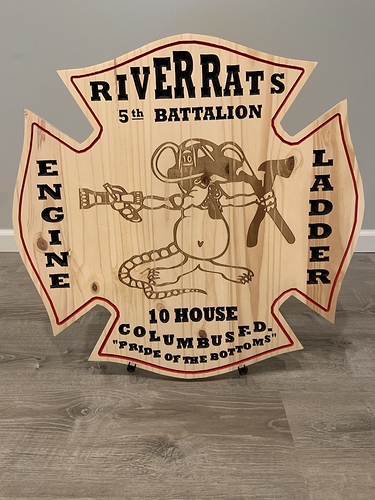
If you have a program for communicating graphically with GRBL, just type it in and save. Set the value writing just $100=79.7342 and press enter. The “secret” formula to get the right numer on the first try is to measure the printed out rectangle and putting it in following “formula”: (Designed_Size / Actual_lasered_size) * Current_resolutionįor instance, if the resolution is set to X = 80 in GRBL, you design 300mm (in the X axis) and it comes out with 301, the formula would be: 300 / 301 * 80 = 79.7342 X and Y aren’t the same value, you must tweak them individually. If it’s more (or less) than it’s supposed to be, tweak the value.
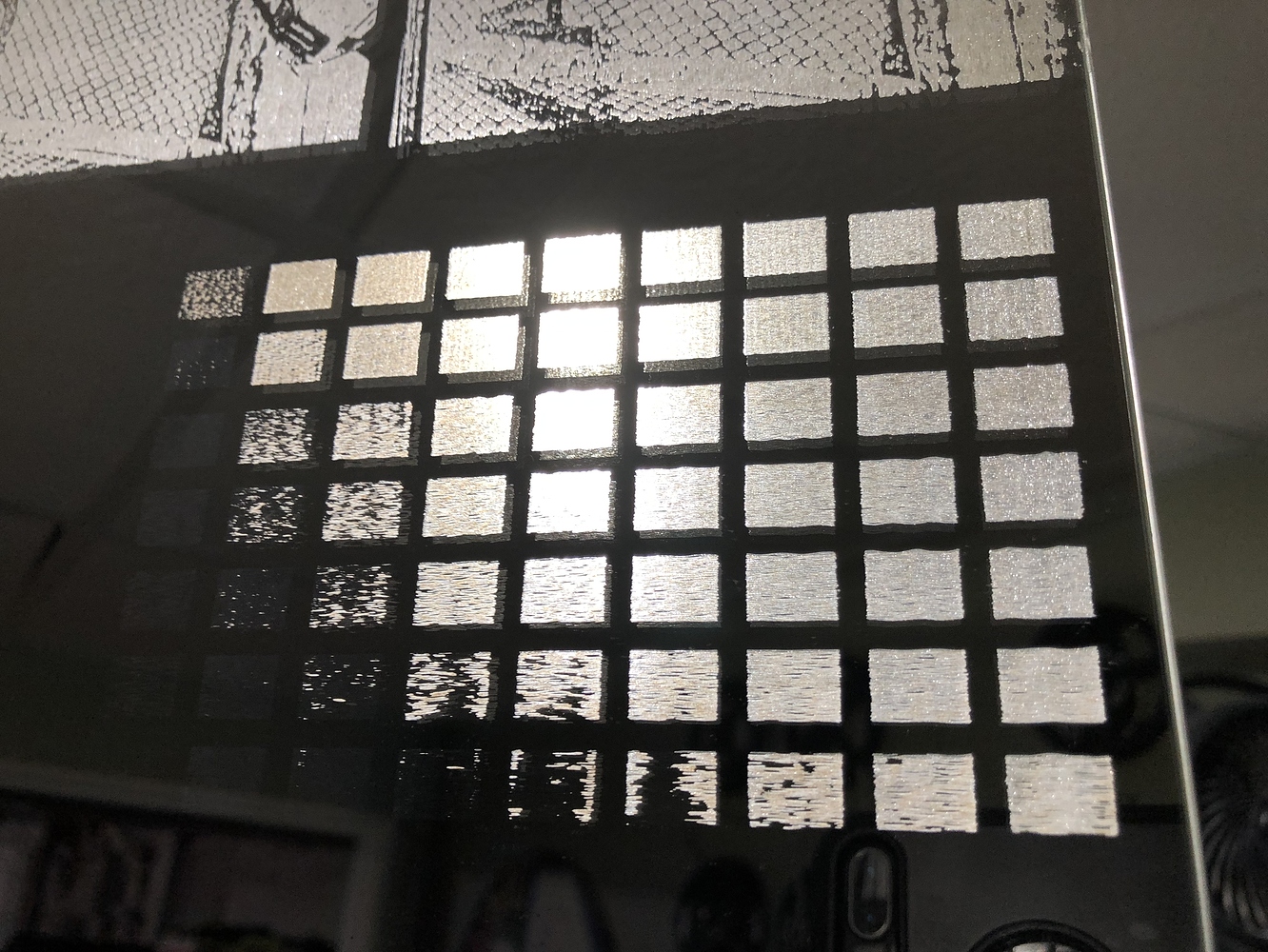
If it meaures 300 perfectly, the value you set is spot on. If it’s printing right with “1600”, don’t change them and just tweak them! Simply design a 300x300mm rectangle or some other size (not to small), laser it and measure it. Start with one of the values above and then tweak them. Basically, this value is obtained by your gear size, microsteps and some other things. According to the attached picture, your stepper resolution probably is wayy to high! The most common is 80 or 160 (at 16 microsteps, check your driver configuration how many you have).
